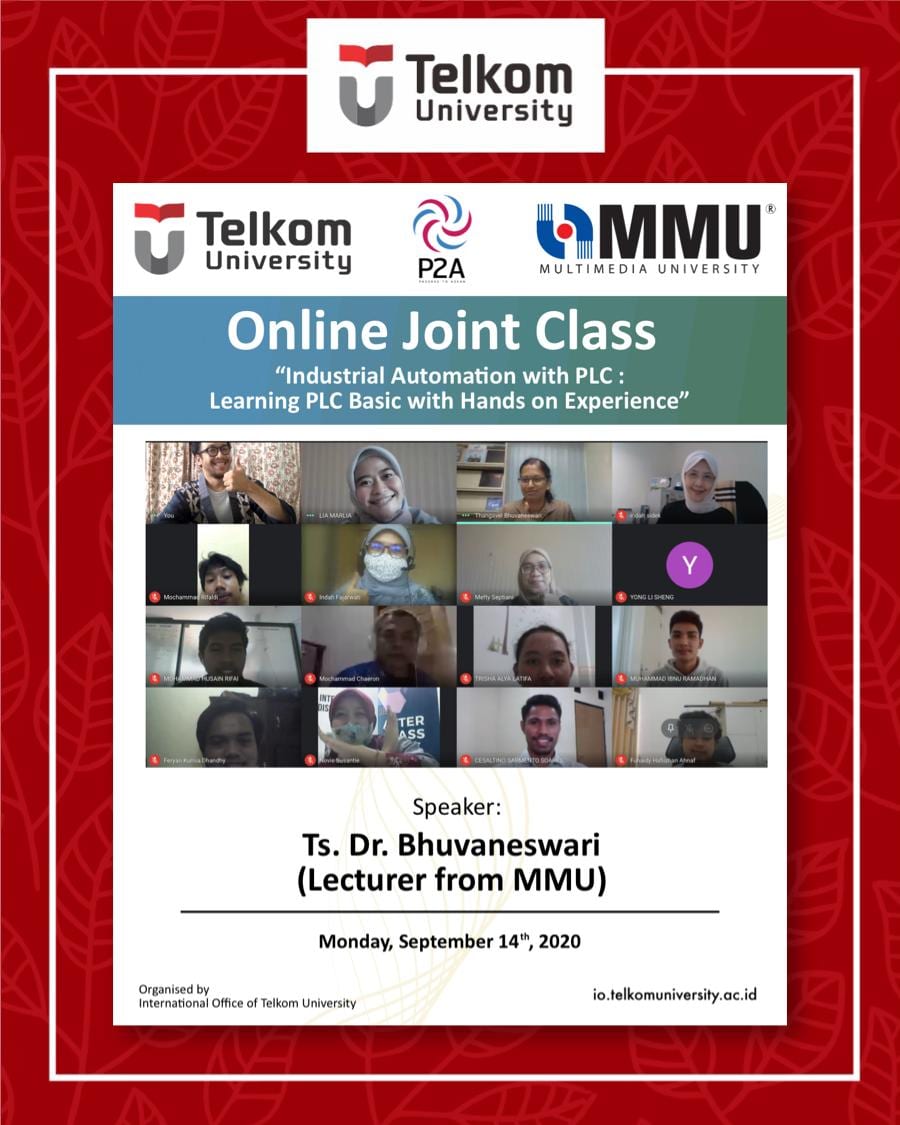
Industrial Automation with PLC: Learning PLC Basic with Hands on Experience, the 14th Online Joint Class Tel-U & MMU
Industrial Automation with PLC: Learning PLC Basic with Hands on Experience, the 14th Online Joint Class Tel-U & MMU. Ts. Dr. Bhuvaneswari, a lecturer of Multimedia University Malaysia was successfully delivered material on Industrial Automation with PLC: Learning PLC Basic with Hands on Experience in the 14th Online Joint Class Telkom University and Multimedia University Malaysia, September 14th, 2020. In her class, Dr. Bhuvaneswari covered definition, history, and types of PLC, PLC system components, PLC programming rules, input and outputs of the PLC. Also, Dr. Bhuvaneswari showed the examples of PLC and demonstrated how to use virtual lab (Allen Bradley simulator from Rockwell automation). After participating in this online class, students were expected to be able to understand the basic concepts of the PLC and its applications in industrial process, to read a PLC ladder diagram and create a simple PLC ladder diagram with timer/counter, and to do simulation using Allen Bradley simulator.
According to Dr. Bhuvaneswari, PLC (Programmable Logic Controllers) is a user-friendly, microprocessor-based specialized computer that carries out control functions of many types and levels of complexity. PLC is also defined as a solid state members of computer family that uses integrated circuits instead of electromechanical devices to implement control function. PLC is capable of providing strong instruction to implement control functions such as sequencing, timing, counting, arithmetic, data manipulation and communication to control the industrial machines and process.
The purpose of PLC is to monitor crucial process parameters and adjust process operations accordingly. It is used extensively because the PLC is easy to set up and program, behaves predictably, and ruggedized. PLC can be programmed (to a degree), controlled, and operated by a person unskilled in operating (programming) computers. Essentially, a PLC’s operator draws the lines and devices of ladder diagrams with a keyboard/mouse onto a display screen. The resulting ladder diagram is converted into computer machine language and run as a program.
Previously, the first PLC is in 1968 that aimed to eliminate the high costs associated with inflexible, relay controlled systems. It was designed according to the following design criteria: 1) Price competitive compared to relay logic, 2) Sustainability in industrial environment, 3) Easily replaceable input and output interface, 4) Easily replaceable for repair, 5) Capability to transfer the data collection to central system, 5) Simple and easily understandable by plat personnel.
Now, the programmable controllers are developed into the following advancement:
- Faster scan times with the help of advanced microprocessors and electronics technology,
- Small, low cost and powerful PLCs which can replace 4 to 10 relays
- Space, efficient high density input/output interface,
- Intelligent expandable distributed processing,
- Facility to connect special interfaces such as thermo couples, strain gauges and fast-response inputs directly to the controller,
- Improved operator interface techniques and system documentation facility.
Before ending the session, Dr. Bhuvaneswari employed mini quiz using kahoot games. This session was intended to check participants’ understanding toward the material given. The quiz was pretty interactive because Dr. Bhuvaneswari reviewed material in every question once the participants submitted the answer.(IO)***